The Spiral Submerged Arc Welding (SSAW) process is a unique welding technique that has been used to join pipes for thousands of years. As technology and techniques have evolved, SSAW has become one of the preferred methods due to its ability to produce strong welds with minimal effort.
In this article, we will explore exactly what SSAW is, how it works, and why it’s such an effective solution for many applications. Well also discuss the various advantages and disadvantages associated with using this type of welding in your project.
Whether youre looking to understand the basics or get into more detailed specifics, this article should provide you with all the information needed to make an informed decision about whether or not SSAW is right for your needs.
Advantages of Using SSAW Pipes
SSAW pipe offers several advantages when compared to traditional straight seam welded (SSW) pipes. SSAW pipes are much stronger and more ductile, making them ideal for applications that require greater strength or flexibility.
The spiral welding process also produces less scrap material than SSW pipe production, which reduces costs and environmental impact. Additionally, the tight tolerance control offered by this process makes it possible to produce large-diameter pipe with an even wall thickness throughout its length.
This offers increased reliability in applications where high pressure or temperatures may be present. Finally, the uniformity of spirally welded pipes allows for faster installation times with fewer joints needed during construction projects.
Quality Control Considerations for SSAW Pipes
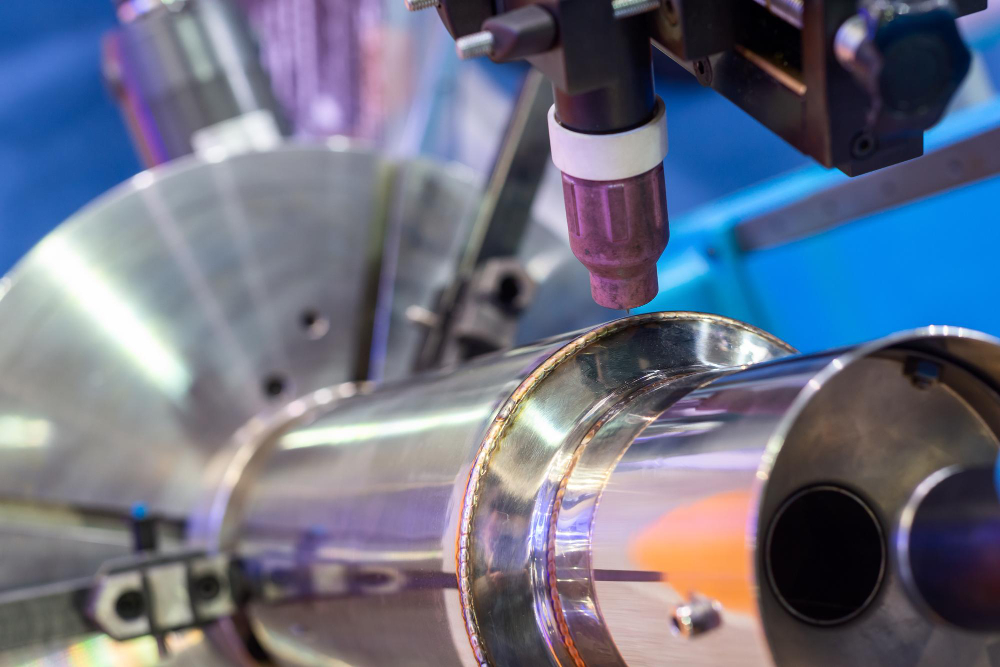
Quality control considerations for SSAW pipes are extremely important to ensure that the pipe meets industry standards as well as the customer’s requirements. Rigorous inspections must be conducted throughout each stage of production, from raw material sourcing up until final product delivery.
Checks should include visual inspection to identify any defects such as welding flaws or surface imperfections, non-destructive testing (NDT) techniques like ultrasonic testing and radiography which can detect internal flaws, and chemical analysis of samples taken from the weld seam. In addition, checks need to be made on wall thicknesses and other dimensional measurements to guarantee accuracy and consistency across all pipes produced.
All test results must then be documented according to international standards for quality assurance purposes. Finally, a hydrostatic pressure test is typically carried out at room temperature to verify that no leakage will occur during operation before shipment takes place.
By following these processes carefully it is possible to make sure that only high-quality SSAW pipes are supplied within the agreed timeframe without compromising safety or reliability levels.
Applications for SSAW Pipes
SSAW pipes are an integral part of many construction projects, as they can be used in a variety of applications. From supporting bridges and piping systems to providing structural support for buildings, the uses of SSAW pipes are vast.
With their strong weld lines and flexibility when it comes to fabrication, these pipes have become increasingly popular for use in various industries. One major application is in the oil and gas industry where they are used for transporting crude oil from offshore rigs or refining plants on land.
They can also be used to transport gases like natural gas over long distances without any loss of pressure due to their impressive strength. Furthermore, SSAW pipes can also be employed in water supply pipelines due to their corrosion-resistant qualities and ability to withstand high temperatures which make them ideal for hot water pipelines too.
The strength and durability that this type of pipe provides make it suitable for other applications such as bridge supports, transmission towers, transportation tunnels, and even foundation piles among others. It’s also possible to customize welding processes depending on the specific requirements making it ideal when constructing structures with complex shapes or sizes since there’s no need for extra fittings or joints during the installation process which saves time and money while offering better security against leaks at joints often caused by traditional welding methods such as arc welding or butt fusion welding techniques. All-in-all SSAW Pipes offer great versatility across multiple industrial sectors with various advantages compared with other traditional methods including cost savings through reduced labor costs plus increased safety due its superior weld line quality ensuring secure connections between different components throughout the entire pipeline system regardless of how large scale project may be.
Conclusion
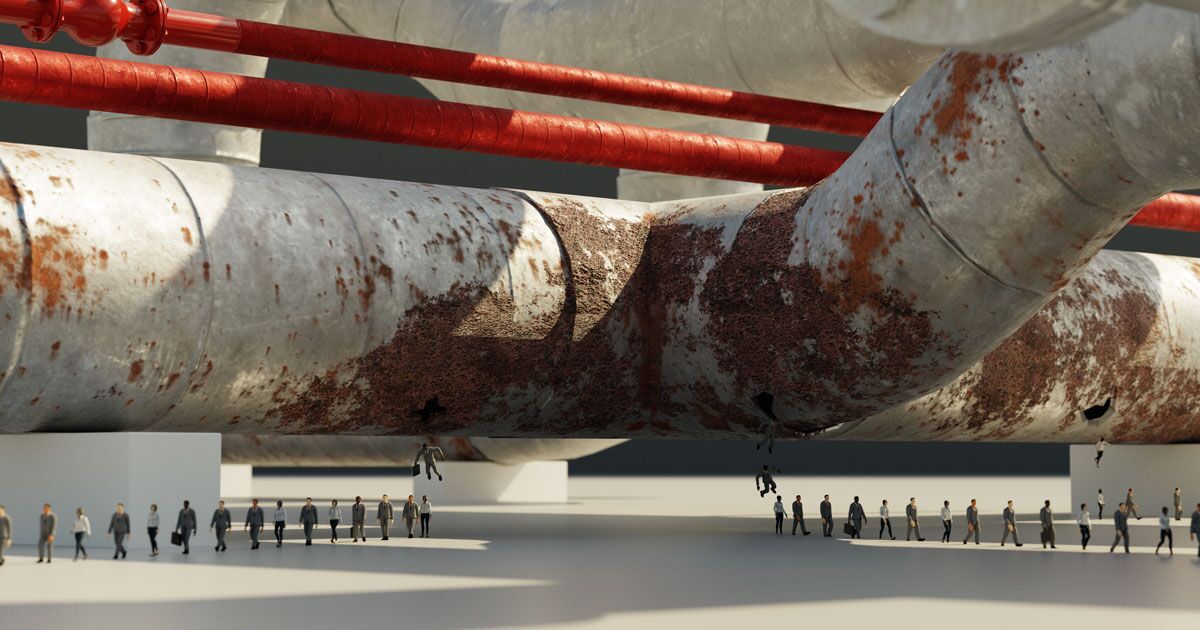
The SSAW pipe, also known as the Spiral Submerged Arc Welding process, is an efficient and cost-effective method for creating welded steel tubes and pipes. This welding process uses a continuously rotating welding machine to create a submerged arc that produces high-quality welds with excellent mechanical properties.
The SSAW pipe has been used in many industries such as oil & gas transportation, construction, automotive manufacturing, and shipbuilding due to its superior strength and durability. Moreover, this welding technique helps reduce the time and costs associated with welding processes by providing better efficiency levels than other methods of tube production.
With its numerous advantages over traditional methods of tube production, it is easy to see why the SSAW pipe has risen in popularity among engineers looking for reliable solutions when it comes to metal fabrication projects.