When it comes to PCB testing and quality control, ensuring functional circuitry is essential. As advancements in technology continue to be made, the complexity of circuit boards grows ever more intricate.
This requires a level of precision and accuracy that can only be achieved through comprehensive testing procedures. Quality control measures ensure maximum efficiency for circuits while also guaranteeing reliability throughout their lifespan.
As such, professional PCB testing and quality control remain an invaluable asset in any electronics industry project today.
Identifying Potential Issues with Circuit Design
Identifying potential issues with circuit design is an essential step in the PCB testing and quality control process. With a comprehensive testing regimen, engineers can detect flaws in board layout, component selection and placement, power delivery systems, and other elements that may compromise the functionality of a printed circuit board.
By analyzing all aspects of the design holistically they can identify weaknesses before production begins so any corrections or changes can be implemented quickly and cost-effectively. To ensure optimal results, engineers need to consider not only current industry standards but also possible future trends that could influence their designs.
Additionally, thorough stress testing should be conducted on prototypes to ensure durability over time as well as environmental factors such as temperature extremes or vibration levels over which the device may be exposed during operation. Ultimately these steps will help confirm that all components interact correctly with one another leading to reliable performance when deployed in real-world applications.
Verifying Component Placement and Electrical Connectivity
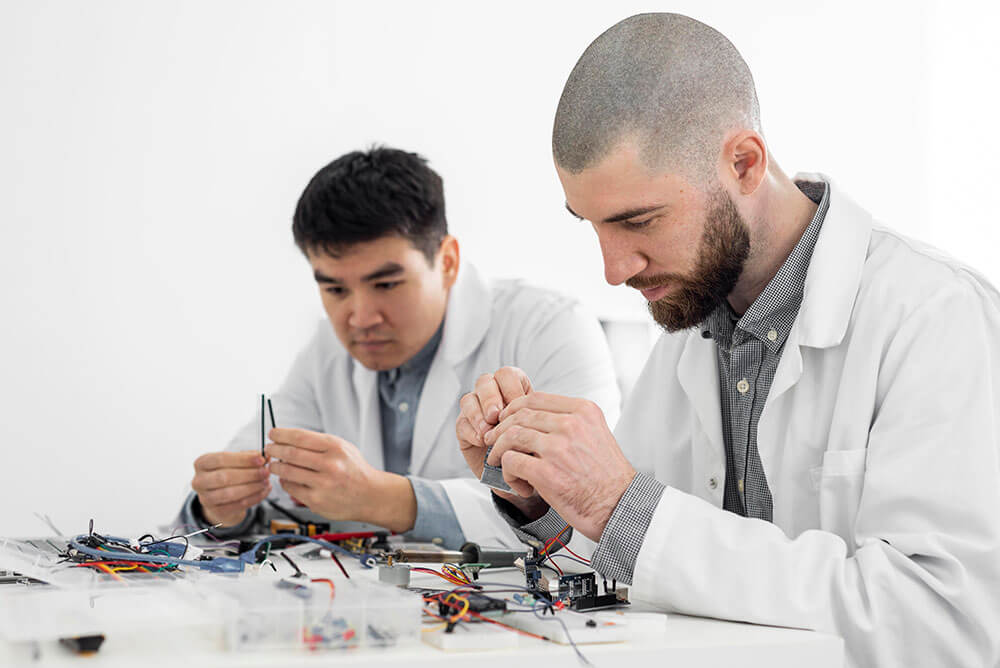
Verifying component placement and electrical connectivity is a crucial part of PCB testing. This process requires testers to inspect all components to ensure that they are correctly placed and soldered, as well as check for any broken or missing parts.
Additionally, each connection must be tested for continuity with the appropriate test equipment such as ohmmeters or multimeters. It’s important to thoroughly examine each circuit element to accurately determine whether the board will function properly after assembly.
By doing this, we can guarantee that our boards are ready for use when they reach their intended destination.
Ensuring Functional Circuitry Through Thermal Analysis, Reliability Tests, and Compliance Standards
Quality control and testing of printed circuit boards (PCBs) are essential for ensuring functional circuitry. Thermal analysis, reliability tests, and compliance standards are all crucial components in the process.
Through thermal analysis, a PCB can be checked to ensure it meets any operating temperature specifications. Reliability tests check long-term performance under different conditions such as vibration, shock, or environmental exposure.
Compliance with industry standards is also necessary; this includes UL certification for safety requirements in most countries as well as other special certifications depending on the intended application of the PCBs. With these measures taken into consideration during quality control procedures, manufacturers can have peace of mind that their products will perform reliably over time and meet applicable regulatory requirements.
Conclusion
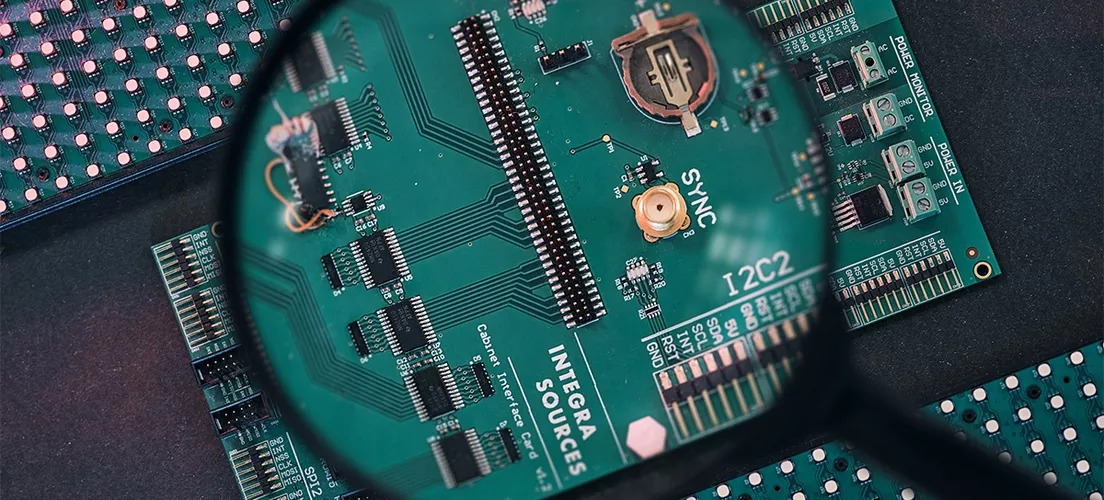
The importance of PCB testing and quality control cannot be underestimated. By ensuring functional circuitry, manufacturers can deliver a product that meets customer requirements with confidence.
Backdrill PCB technology is an effective way to ensure functionality by reducing the amount of electrical noise while increasing the reliability and performance of the circuit board. Quality control through rigorous testing ensures that customers receive products that meet their expectations and perform as expected in the field.
With proper design, manufacturing processes, inspection techniques, and comprehensive testing procedures in place, companies can feel confident about delivering high-quality products to their customers every time.