The automotive industry is constantly evolving, and so too are the techniques used to design cars. One important process for creating intricate parts is press brake technology.
Press brakes allow manufacturers to create complex geometries with precision and accuracy. With these tools, they can craft components that would be impossible or difficult to produce with traditional methods.
In this article, we will discuss advanced press brake techniques in automotive design and how they can help navigate the complexities of modern car manufacturing.
Understanding Complex Geometry in Automotive Design
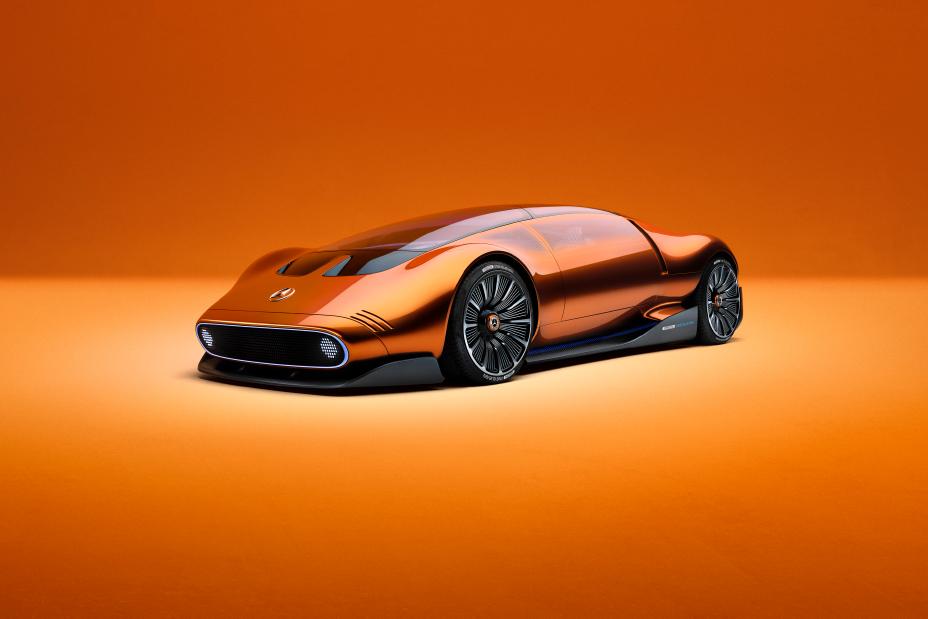
Auto manufacturers are increasingly requiring new and complex geometric shapes for their vehicles, creating a demand for more sophisticated press brake techniques. To keep up with the competition, auto designers must understand the complexities of working with geometry in automotive design.
In particular, understanding how to accurately calculate angles and radii is essential when trying to achieve desired results from press brakes. Additionally, designers must have an understanding of geometry principles like parallelism and perpendicularity which can be used to create uniform bends throughout a vehicle’s body parts. Furthermore, they should also know certain tricks such as using different tooling or multiple passes on the same part to ensure accurate bending results every time.
Finally, designers must take into account any potential problems associated with complex geometries like material deformation or uneven edges before starting production so they can make adjustments accordingly. By having a comprehensive grasp of all these factors related to advanced press brake techniques in automotive design, auto designers will be well-equipped to navigate through even the most intricate geometries successfully.
Utilizing Advanced Press Brake Techniques

When automating the production of complex automotive parts, press brake technology is a valuable tool. Press brakes are designed to bend and form metal in various shapes and sizes, allowing for increased efficiency while ensuring accuracy in the fabrication process.
Advanced press brake techniques allow manufacturers to produce custom parts with intricate geometries that would be impossible otherwise. The use of advanced press brake techniques allows for more precise control over the shape of components than traditional methods alone.
This greater level of detail can be used to create unique designs that meet customer specifications precisely or increase product performance by reducing weight without sacrificing structural integrity. The ability to craft these detailed components quickly and cost-effectively enables manufacturers to stay ahead of their competitors by providing higher-quality products faster than ever before.
By utilizing both conventional and advanced press brake techniques, automotive designers can navigate complex geometries for even the most demanding projects while maintaining tight tolerances throughout production runs. With this combination of precision and speed, engineers have access to an unprecedented level of freedom when it comes to creating innovative solutions as they explore new ways to push design boundaries further than ever before.
Applying Technical Guidelines for Process Optimization
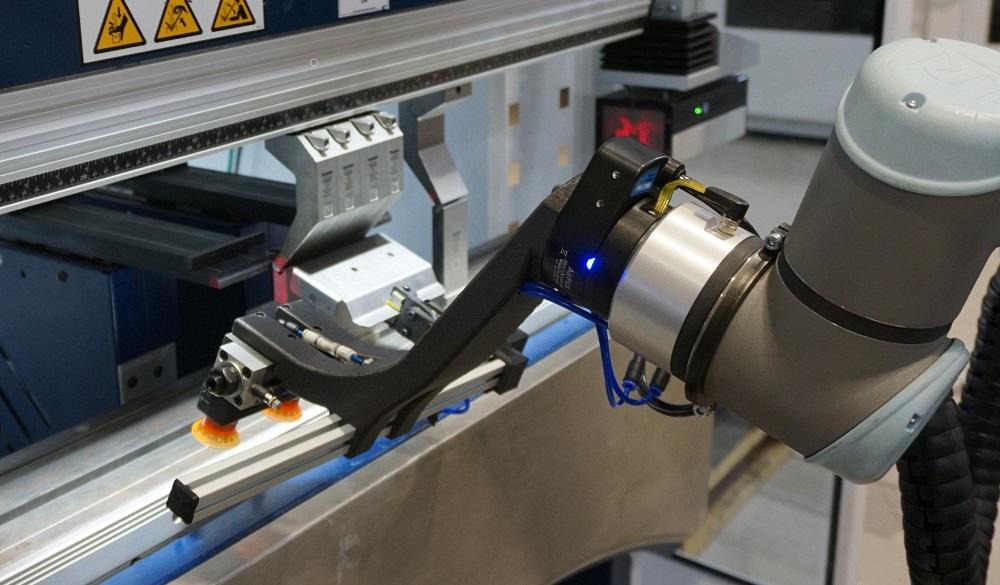
When utilizing advanced press brake techniques in automotive design, technical guidelines for process optimization are essential. By following a prescribed set of criteria, designers can ensure that their plans maintain the highest level of precision and accuracy.
Technical guidelines provide an organized framework to assess product performance before and after production, as well as identify areas for improvement. Moreover, they allow automotive engineers to create reliable designs that adhere closely to safety regulations while also reducing costs through streamlined processes.
With this knowledge in hand, engineers can develop automated processes with greater efficiency and flexibility than ever before. Altogether, these technical guidelines enable manufacturers to produce highly complex geometries with fewer resources while meeting the exact specifications demanded by the industry.
Evaluating Potential Challenges of Working with Complex Geometries
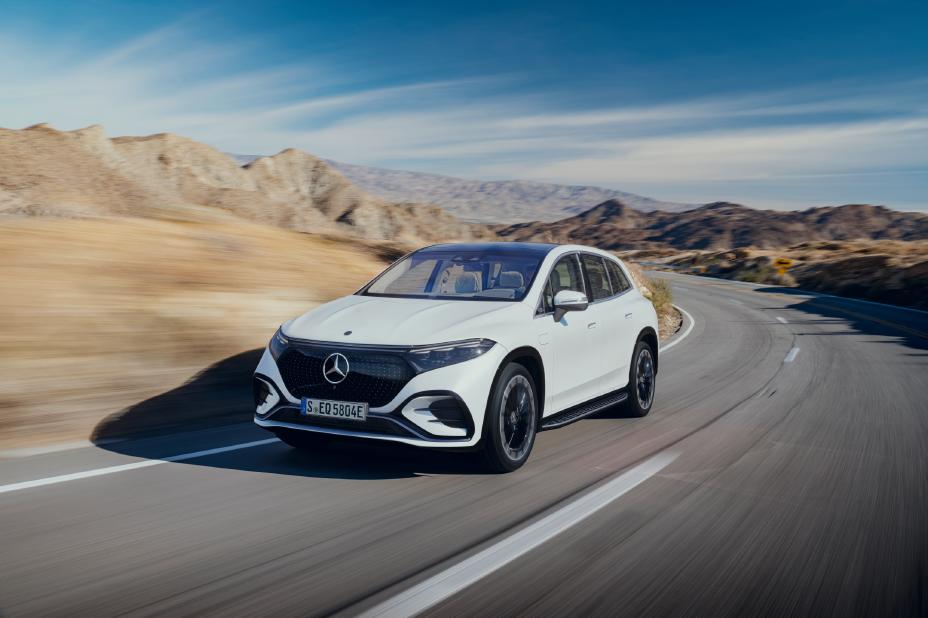
When it comes to working with complex geometries, one of the main challenges is that the process requires a high level of precision and accuracy. This means that press brake operators must have an intimate knowledge of how their machines work and be able to accurately control them for each job.
It also requires a higher degree of skill than working with simpler shapes as any inaccuracies can result in costly mistakes and delays. Additionally, when dealing with complex geometries, the number of bends needed may increase significantly which adds to the complexity and cost associated with operations.
Moreover, it is important to consider tooling selection for these types of jobs as slight variations in tool size or shape can have a significant impact on final results. Ultimately, understanding all potential challenges associated with working with complex geometries is essential for successful automotive design projects.
Conclusion
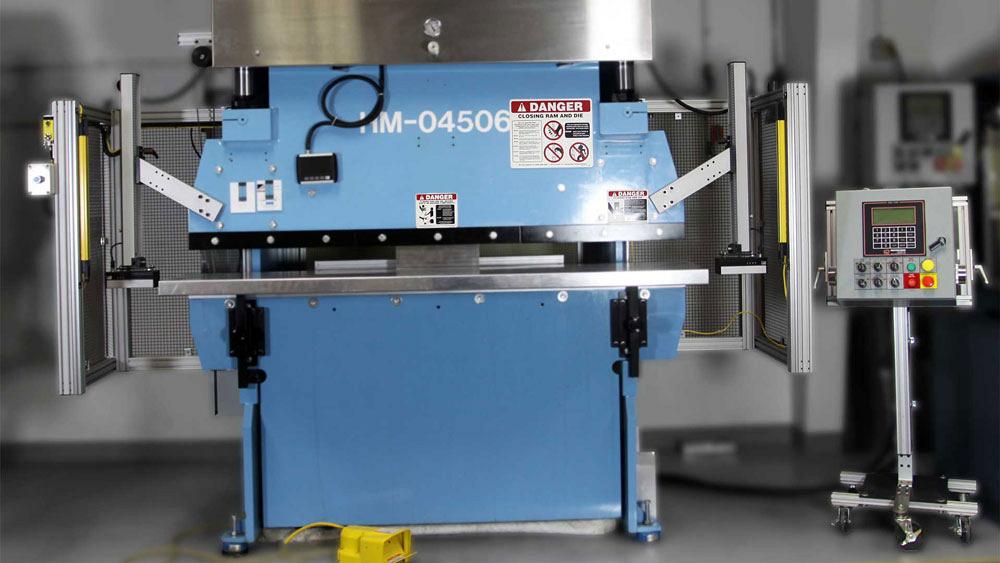
The increasing complexity of automotive designs has put a strain on traditional press brake techniques. But with advanced CNC press brake technology, fabricators can now navigate the complex geometries and precision required for these parts with ease. This modern approach to pressing metal enables manufacturers to create high-quality products without compromising design or performance.
As such, CNC press brakes are becoming an essential tool in the automotive industry, allowing engineers to push boundaries while maintaining accurate results every time.